All copper contact are gold plated.
Does that mean you’re paying someone rather than doing yourself?
Ok yeah that’s what I thought. There are connector sold now that are pure copper with no plating. Some say it can sound very good.
I do not own a temperature controlled soldering iron, so a friend does it. He will get a pence for it.
You don’t need to own a temperature controlled soldering iron for cables… all irons have thermostats… the key thing is a sensible wattage and appropriate tip for the job in hand. Most good irons come with a few tips or are easily available. Use a jig and/or ‘helping hands’ and I find an illuminated magnifier helpful.
I have soldered ‘professionally’… I only solder for personal use now. It’s not difficult, especially if not manually soldering surface mount, don’t assume a professional soldering job is better than yours if you practice and take time to understand what you are doing. I always recommend using separate additional flux.
This is what I spend most of my soldering time on these days and it is a royal pain. Even if you have years of experience, SMC soldering is not really tolerant of having slightly “off” days. I had to recap a control board on a proprietary optical device last night that ended production about 20 years ago. Between constant interruptions from kids and slightly too much coffee, every surface mount cap went on crooked. Every damn one. And I’ve done this more times than I can count.
I’d say SMC soldering is only surpassed in difficulty by dealing with a PCB that has multiple lifted pads and traces due to someone else’s shoddy work.
The things we do to keep ancient bits of kit running.
Yes, that is invaluable especially with things like stranded cable.
As for SMSs, a lot depends on components and layout - but something to press them gently in place is essential!
Howzit Lucifer, my DIY IC specs are …
Cable - Mogami W2549
Conductors x2 0.339mm² (22AWG) 30 strands 0.12mm Neglex OFC
Shield/screen 64 strands 0.18mm Neglex OFC Spiral Wound
Insulation XLPE (Cross-Linked Polyethylene)
I sellected the cable to get low capacitance which is 76pF/m core to screen 11pF/m core to core.
I also sellected the cable to use screen as a common -ve return, as that followes the Naim configuration with 2 channel (ch1 & ch2) with a common ground return (-ve). Additionally the Naim applied DIN plug standard uses only 1 pin for the common ground return (-ve).
DIN Plugs - Neutrik REAN NYS322
DIN 180’ 5-pin
Silver plated connection pins
Thank you. Very nice. Have you compared that cable to the Hiline?
Hi @ChrisSU, yes, I tried a 5m, 1.2m & my own required 0.37m & 0.28m.
First I have never read any Naim or Chord technical reasoning for the claimed adverse effects.
The only parameter that I’m aware of that can effect performance in a typical/normal IC is excessive capacitance as longer lengths with higher capacitance can get close to <20kHz roll off.
My reasoning for a shorted IC was if 1.2m and its capacitance is OK, then less would at least have no detrimental effect.
My testing showed up very little, no difference that I could detect or measur between 1.2m & 0.28m. Maybe a slight change with the 5m length, but nothing that I could measure.
The 0.28m length from CDX2 (now NDX) to Supernait
Core to Core (crosstalk) = 3pF.
Core to screen = 21pF.
Yes, I prefered mine over HiLine, but I also prefered AR over HiLine.
I also didn’t like the construction quality of HiLine
Yes that is an interesting question. Could be Rhodium since they use Rhodium on the Schuko.
Rhodium has a higher lustre. I would guess it matches the IEC inlet on the boxes which is nothing fancy. But until they say we won’t know.
Ah I see it was only a “bloke guess” as we say here in Sweden.
This seemed to work well for me as well. It has been a while since the DIY days but I know that I liked this cable. It was a converted Acoustic Research Pro 3.5mm to 2 x RCA. I simply replaced the 3.5mm with a locking DIN, with red + ch1, white +ve ch2 and the shield/drain to the -ve pin. The DIN had copper alloy silver plated pins (probably by Switchcraft?).
On the other side the shield ended somewhere and wire leads emerge at the RCAs’ -ve (I believe NAIM does similar in some of their ICs?)
I think the basic cable was in their short lived, very affordable but good Pro HT series. The cheaper Performance series were to be avoided apparently…
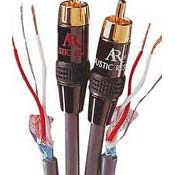
“Directional, Balanced-line oxygen-free copper cable with precision machined gold-plated connectors Aluminized Mylar shield overlaps for 100%” The cores look like 24AWG.
I found another DIY RCA to 5 pin DIN (with Neutrik Rean connectors) made with the Mogami 3106 which also must have been good.
I agree, the soldering is very important. Check temperature vs. the solder you use if you want to optimize. I’ve re-purposed old lavenders with very light RCA’s and have used LMP solder ever since Jean Hiragas listening tests on solder in L’Audiophile 40 years ago - I’m sure there are better stuff around today.
My rean 5 pin din connectors have now been sent from the dealer and will hopefully arrive next week. I’m excited to hear how the Neotech Nemoi 1220 will work as an interconnect with those connectors instead of RCA as I tested with RCA nad found the Hiline to be a better choice. It still might be but I couldn’t leave that stone unturned.
it’s still a time vs cost benefit balance though. I make up all sorts of leads. Subwoofer cables, non main source interconnects etc with decent cable stock and plugs but standard 60:40 tin-lead solder. The really decent solder for audio applications is quite expensive and I’d never justify a roll of it unless I’m making up 200 cables. I think a small drum of lead-tin is like $30 last time I bought one. But the same size drum of silver exotica is like $800.
For this reason, I strike a balance. I’m really happy with my own work but I’m also happy to save money where I can but buy a HiLine (or whatever) for my main source. You definitely get to a point where a cable seems like a lot of money but when you factor in your time and the other bits you might need, that expensive cable actually costs less.
99% of the soldering I do is on PCBs for things I cannot go out and buy off the shelf.
I will leave the OP with this though: learning to solder is a brilliant DIY skill to have. If just for being useful in home repair. The number of household appliances that can be made to last your whole lifetime if only you know how to solder, recap, and find things on Radio-Shack online. If your friend will teach you and show your safe recapping procedures, it’s really something your won’t regret.