See my post above. They are designed a little bit differently to the classic power amps and purposely made more tolerant.
My understanding is that if an amp has no inductor in the output stage, it can use the inductance of the speaker cable instead. So the amp either needs the correct type and length of speaker cable, or it doesn’t, and the information in the various Naim manuals would seem to reflect that. The separate power amp manuals say you need 3.5m of NACA5 or more. The Uniti and Nait manuals do not.
Perhaps it’s actually not as simple as that, but I have never seen an explanation that suggests it is less clear cut.
Ok so might be worth me trying some NAC A5 cable in stead of my cord Rumour. Is 3.5 MTR the minimum as speakers are either side of the unit wear the Nova is so will be to much cable so is it ok to coil it up?
Mike
Don’t coil it, each turn (circle) adds inductance, especially bad if one side is coiled & the other side not, that makes the channels unbalanced.
The correct way is to fold it.
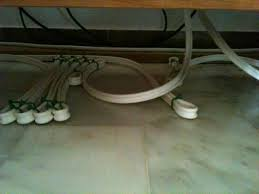
I’ve just bought some new NACA5 and have made it up with Naim plugs, lots of cursing later it’s up and running on my SN3. What should I expect, if anything, in terms of burning in period? It seems a little more forward then my previous Audioquest cable
When you get it all right - perfect soldering, SA8 plugs, proper movement within the plug housing - NACA5 is wonderful but it does take ages to fully burn in. It’ll sound pretty good after a few weeks but it can take 6 months or more of proper play before the sound really blooms and you get real depth and focus. I’m convinced this is one reason why some don’t like it; it’s judged too early before it’s had a chance to really shine.
Ok thanks Richard, I’ll stick with it! I’m fairly handy making up cables and soldering etc but I found this quite tricky, I’m not 100% happy so will probably redo, the bare cable is such a tight fit in the slot it’s difficult to get the solder to run right down through it without over heating it and then melting the insulation, I’m using an 80w iron. Will experiment further until I get it right
I use a 100w & found that is OK but my 50w isn’t.
Its temp controlled & I set it at 325’C for 60/40 multicore with joints such as banana pins. I insert the pins in a purpose made wood holder, a 4mm hole drilled in a bit of softwood, it’s ideal (best) for a firm/steady hold on the pin & it retains a lot of the heat. A wide chisel tip profile is ideal to push the NACA5 cable into the pin slot.
I use a Butane torch.
Scarey, who needs temperature control??
Seriously though, I’ve used butane & even oxy/acetylene when pushed in emergency/field situations. The nice thing about an iron with big wattage & temperature control is a fast made joint & the insulation is not at much risk of damage.
It works great for me. I get a nice small blue flame and it heats the cable and pin up quickly. My dealer taught me that trick.
Thanks Mike, I’m using a similar setup with some timber and 4mm holes, I’m also squishing the copper slightly with a pliers to help insertion. I think the 80w is ok, there’s plenty of heat it seems its just getting the solder to flow all the way through is my difficulty, I might try pre tinning and see does that help
Don’t pre-tin - you’ll never get the copper to fit neatly in the plug slot. Shape the copper strands by compressing with pliers and it should fit in.
Also, worth using the same type of solder that Naim use - Multicore Crystal 505 - or similar.
That sounds very much like it ain’t hot enough, the wire is conducting heat away too fast, its either not enough watts or too cool when you start. Maybe leaving the iron to cook for a while longer might help.
If it takes really that long for NACA5 to burn in, I’d consider buying second hand
I use a 175 watt iron for doing my NAC A5 with SA8 plugs. It does the job quick and practice will be required but once mastered it will sound absolutely fantastic. Practicing on some old stuff first is highly recommended and will save a lot of heart ache…
Agreed, you need enough wattage to heat up the exposed copper fast, before the heat has time to conduct down the wire inside the sheath. Apart from melting the insulation, it can wick solder down the wire too. In more flexible cables, you can feel that the end bit of cable has gone rigid if this happens.
I’d say you need a fair bit more than 80W for this, I know some like to use 200W irons.
You have to be very quick with powerful irons (almost instant) or the plating will blister and render the pin(s) useless and I agree, the quicker the better.
Started from scratch today with a new approach and some better tools, much better job and sounding really good. Just need to get better plugs for speaker end - any recommendations?
Good old fashioned Deltron bananas do a good job. They’re cheap, too. If your speaker has gold plated sockets, I’d use gold plated plugs. Otherwise go for the standard nickel plated version.
You could also use Naim plugs, but if the spacing isn’t right, remove the black plastic box. In which case you can use heatshrink tubing to cover the exposed metal.